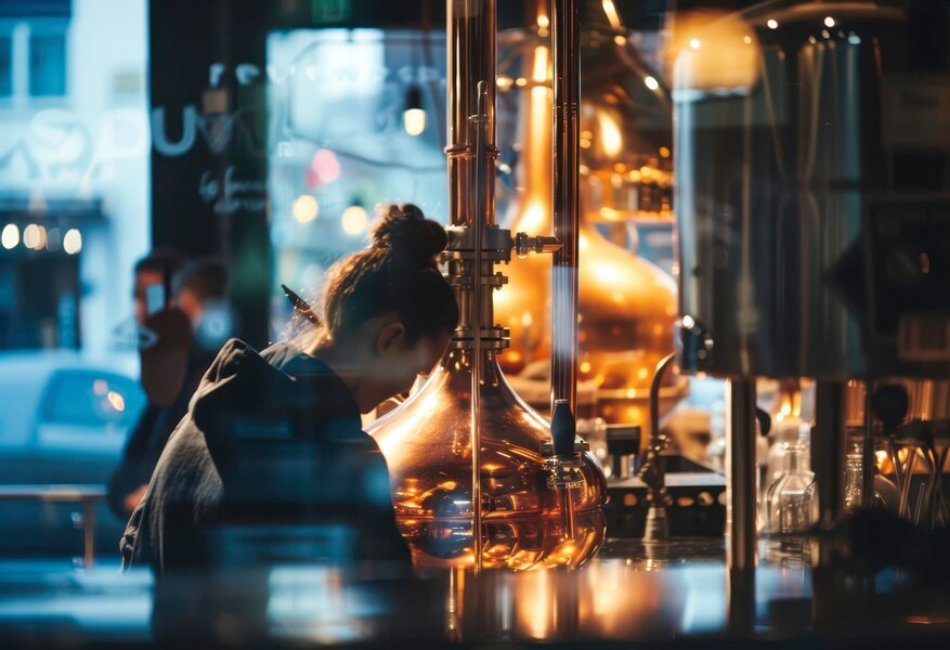
Fuel oil plays a crucial role in various industrial settings, powering everything from machinery to heating systems. In the United Kingdom, where industries often rely on this energy source for their operations, understanding best practices for its usage is essential to ensure efficiency, safety, and environmental compliance. This article explores the best practices for using fuel oil in industrial settings, focusing on optimal performance, cost-efficiency, and regulatory adherence.
Understanding Fuel Oil Types and Their Applications
Before delving into best practices, it’s important to understand the types of fuel oil commonly used in industrial settings:
- Heating Oil (Gas Oil): Typically used for heating and powering equipment. In the UK, it often refers to kerosene or similar refined products.
- Diesel Fuel: Used for engines and machinery, diesel fuel can vary in its composition and properties, such as standard diesel and ultra-low sulfur diesel (ULSD).
- Industrial Fuel Oil: Includes heavier oils like marine fuels and residual oils, used in larger industrial boilers and turbines.
Each type has specific applications and characteristics, which influence how it should be handled and used.
Best Practices for Fuel Oil Usage
1. Proper Storage and Handling
A. Storage Tanks:
- Location: Store fuel oil in a secure, well-ventilated area. In the UK, tanks should be positioned to minimize environmental impact and comply with local regulations.
- Material: Use tanks made from corrosion-resistant materials. Steel tanks should be coated or lined to prevent rusting.
- Maintenance: Regularly inspect tanks for leaks and signs of wear. Implement a routine maintenance schedule to address any issues promptly.
B. Handling Procedures:
- Training: Ensure that all personnel handling fuel oil are trained in safe handling practices and emergency response procedures.
- Pumping: Use properly calibrated pumps to avoid overfilling and spillage. Install automatic shut-off systems if possible.
- Spill Prevention: Implement measures to prevent spills, such as using spill containment pallets and secondary containment systems.
2. Efficient Fuel Usage
A. Equipment Calibration:
- Regularly calibrate and maintain equipment that uses fuel oil to ensure optimal performance and fuel efficiency.
- Conduct periodic performance audits to identify and address inefficiencies.
B. Fuel Quality:
- Ensure that the fuel oil used meets the specifications required for your equipment. Poor-quality fuel can lead to reduced performance and increased maintenance needs.
- Use additives if necessary to enhance fuel properties and prevent issues such as clogging or corrosion.
C. Monitoring and Control:
- Implement a fuel management system to track usage and monitor fuel levels. This can help in identifying trends and potential issues early.
- Analyze fuel consumption patterns to optimize usage and reduce waste.
3. Health, Safety, and Environmental Compliance
A. Safety Measures:
- Protective Gear: Require the use of appropriate personal protective equipment (PPE) when handling fuel oil.
- Emergency Response: Develop and regularly review emergency response plans for fuel oil spills and accidents. Ensure that all employees are familiar with these procedures.
B. Environmental Regulations:
- Compliance: Adhere to local environmental regulations regarding fuel storage, handling, and emissions. In the UK, this includes regulations set by the Environment Agency and local councils.
- Waste Management: Properly dispose of any waste products, such as used filters and contaminated fuel, in accordance with legal requirements.
C. Pollution Control:
- Implement measures to minimize air and water pollution from fuel oil usage. This includes using low-emission equipment and adopting practices that reduce the risk of spills and leaks.
4. Cost Management
A. Fuel Purchasing:
- Supplier Selection: Choose reputable suppliers who offer competitive pricing and high-quality fuel. Consider establishing long-term contracts to lock in favorable rates.
- Bulk Buying: Purchasing fuel in bulk can reduce costs. However, ensure you have adequate storage capacity and systems in place to handle larger quantities.
B. Efficiency Improvements:
- Invest in energy-efficient equipment and technologies that reduce fuel consumption. This can lead to significant cost savings over time.
- Regularly review and adjust operational practices to enhance fuel efficiency and reduce unnecessary expenditure.
C. Financial Planning:
- Budget for fuel costs as part of your overall operational expenses. Monitor fuel expenditures regularly and adjust your budget as needed to accommodate fluctuations in fuel prices.
Practical Examples of Best Practices
Case Study 1: Manufacturing Facility
A manufacturing facility in the UK implemented a comprehensive fuel management system to optimize its fuel usage. By regularly calibrating equipment and monitoring fuel consumption, the facility reduced its fuel costs by 15%. Additionally, the facility invested in training programs for staff, which led to a significant decrease in fuel-related accidents and spills.
Case Study 2: Power Generation Plant
A power generation plant adopted advanced pollution control technologies to comply with stringent environmental regulations. The plant installed low-emission burners and upgraded its fuel storage tanks to minimize leaks. These measures not only ensured regulatory compliance but also improved operational efficiency and reduced environmental impact.
Conclusion
Effective fuel oil management in industrial fuel settings requires a combination of proper storage and handling, efficient usage practices, adherence to safety and environmental regulations, and cost management strategies. By implementing these best practices, industries in the United Kingdom can ensure that their fuel oil usage is optimized for performance, safety, and cost-efficiency. Regular review and adaptation of these practices will help in maintaining high standards of operation and compliance in an ever-evolving regulatory landscape.